How Leather is Made
OVERVIEW (VISION D’INSIEME)
The transformation of animals hides into a durable and supple material called “Leather” is an art developed over thousands of years. The natural availability of the hides as a by-product from hunting, and the benefits from having the finished product, have made its development part of culture worldwide.
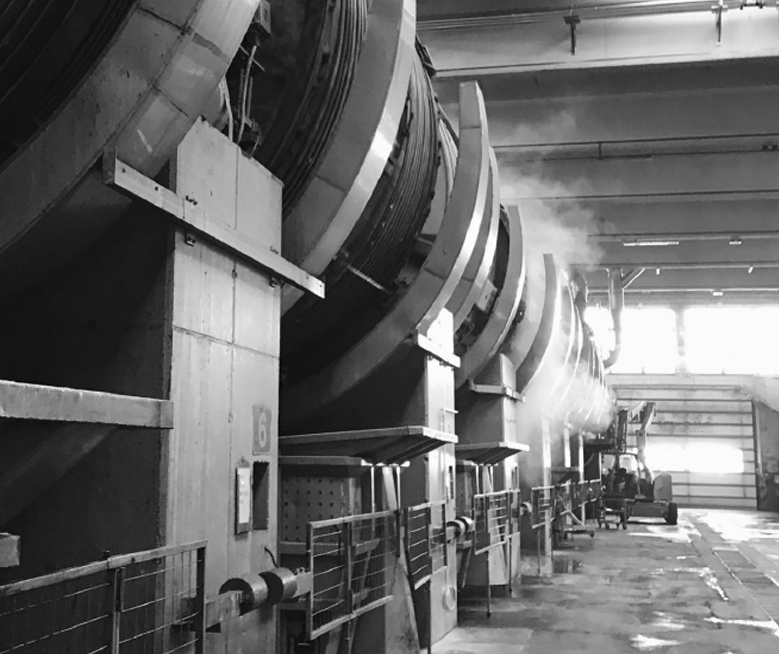
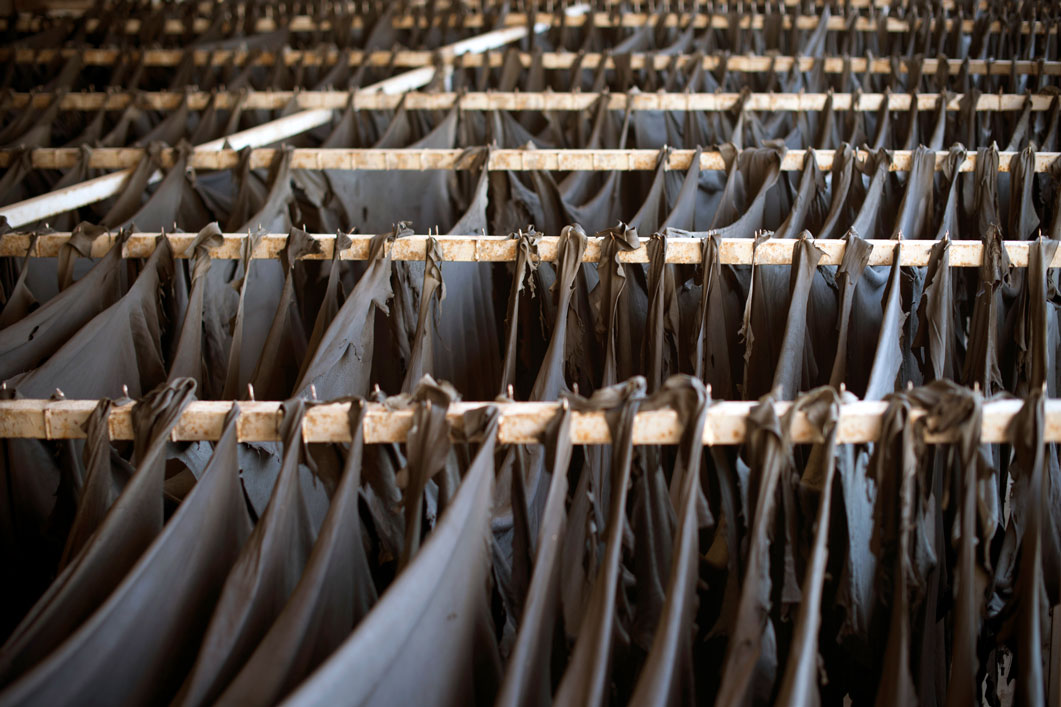
ORIGINAL MATERIAL SOURCING
Quality starts with the selection and grading of the primary material, known as Rawhides. All our hides come from farming for beef and dairy. They come from European sources that have strict controls on animal management and environmental impact.
AT THE BEAMHOUSE – REPARTO DI RIVIERA
The Bundles of the selected hides go to a specialist pre-production workshop known as a Beamhouse. There is a saying “leather is made in the Beamhouse,” and the tasks performed here are crucial for the product’s final quality.
SPLITTING (SPECCATURA) – GETTING TO THE TOP GRAIN
Bovine rawhides can be up to 5mm thick, which is too much for an artisan to handle in upholstery and design applications. The splitting process reduces this thickness and gets the best leather from the rawhide, which needs to be less than 1mm for some of our articles.
OTHER PRE-TANNING PROCESSES
Though the rawhide has been through a variety of processes, there are many more processes that are available to the leather creator. Below are a few of the more widely used;
FIRST TANNING (CONCIA)
The rawhide still needs to become a stable leather that will not perish, and the Tanning process achieves this. This process is not primarily concerned with adding colour or changing the handle (though these may be a side effect) but making sure that the hide’s structure is fixed and stable to create an article that will last. It is only at this point that it can be called Leather.
DYEING (TINTURA)
After tanning, the next step is dyeing through. This is done in dye–stuff . The leather is immersed in a dye bath in rotating barrels, hence the name Drum Dyed. The dye must be fixed and excess colour must be rinsed out to prevent later dye transfer from leather (known as Crocking).
SORTING THE CRUST LEATHER (SCELTA IN CRUST)
The leather then undergoes a Quality Check once the major processes have been completed. The hides are graded designated to the final steps. Hides which do not have significant blemishes or marks at this point can proceed to the Full Aniline process.
FINISHING (FINITURA IN PELLE)
The perfecting touches are made in finishing, and this is where the character of the hide really emerges. This process can be exceptionally time consuming, especially for the subtle artisan work, that gives luxury leather its distinctive look and feel.
FINAL QC (SCELTA IN FINITO)
The QC (Quality Check) is a rigorous visual check for defects and blemishes and determines the area of the hide. The hide is graded for use; there are allowances for small holes and irregularities that might affect the panel sizes. Qualified staff proceed with a final Quality Check (QC) and selection before measuring. After this, the hides are carefully wrapped, packed, and sent on their way to their new home.